辊压机中减速机
来源:减速机知识 发布时间:2025-07-02 17:28:10 阅读:3434次
摘要 —— 辊压机中减速机的关键技术解析与效能提升策略在水泥、冶金、矿山等行业中,辊压机作为粉磨系统的核心装备,其运行稳定性直接影响生产效率和
一站式自动化配套零部件 > 厂家直销
德立元专业的技术团队,品质保障
辊压机中减速机的关键技术解析与效能提升策略在水泥、冶金、矿山等行业中,辊压机作为粉磨系统的核心装备,其运行稳定性直接影响生产效率和能源消耗。而减速机作为辊压机动力传输系统的"心脏",承担着扭矩传递、速度调节与载荷分配的关键任务。本文将深入探讨辊压机减速机的技术特性、选型要素及创新应用,为行业用户提供专业参考。
一、减速机在辊压机系统中的核心作用
辊压机通过高压料床粉碎原理实现物料破碎,减速机在此过程中需要承受周期性冲击载荷和持续重载的双重考验。其核心功能体现在三个方面:
大扭矩转化能力
匹配主电机的高转速特性,将输入功率转化为低速大扭矩输出,确保辊面线速度稳定在0.8-1.5m/s的工艺范围。某型号Φ1800×1000辊压机的减速机输出扭矩可达650kN·m,转化效率超过96%。
动态载荷调节机制
内置弹性扭力杆结构可缓冲物料硬度波动引起的冲击,通过扭矩限制器实现过载保护,将瞬时冲击载荷控制在额定扭矩的180%以内。
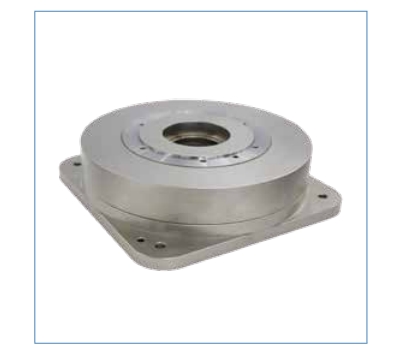
精密传动保障
行星齿轮与圆锥齿轮组合传动系统,配合微米级加工精度的硬齿面齿轮,确保传动误差小于3角分,有效降低辊面偏磨现象。
二、辊压机减速机的技术演进路径
1. 结构设计创新
现代辊压机减速机采用三级传动架构:第一级螺旋锥齿轮实现垂直换向,第二级平行轴齿轮完成主要减速,第三级行星齿轮进行扭矩倍增。这种模块化设计使传动效率提升至98.2%,同时降低轴向尺寸15%。
关键参数对比:
技术指标 |
传统结构 |
新型三级传动 |
传动效率 |
94-95% |
97-98% |
轴向尺寸 |
2800mm |
2380mm |
重量 |
32吨 |
26吨 |
维护周期 |
6个月 |
12个月 |
2. 材料与工艺突破
齿轮材料升级为18CrNiMo7-6渗碳钢,表面硬度达到HRC60-62,芯部保持HRC35-38的韧性。采用数控成型磨齿工艺,齿面粗糙度控制在Ra0.4μm以下,接触斑点超过85%。
3. 智能监控系统集成
集成振动、温度、油液多参数监测模块,通过边缘计算实时分析轴承状态(如图1)。某水泥集团应用预测性维护系统后,非计划停机减少62%,备件库存降低40%。
三、高效选型与运维策略
1. 选型计算模型
根据辊压机规格计算所需减速机参数:
扭矩公式
T=9550×P/(n×η)
其中:
P-电机功率(kW)
n-输出转速(rpm)
η-传动效率
实例计算
某辊压机配置800kW电机,输出转速22rpm,传动效率97%:
T=9550×800/(22×0.97)=325,000N·m
需选择扭矩容量≥350kN·m的减速机型号。
2. 润滑系统优化
推荐使用ISO VG460合成齿轮油,设置双联过滤器(精度β≥200)和恒温控制装置。油液清洁度需满足ISO 4406 17/15/12标准,油箱配置磁性吸附器捕捉磨损颗粒。
3. 故障诊断技术
建立振动频谱数据库,重点关注特征频率:
齿轮啮合频率:Z×n/60 (Z为齿数)
轴承故障频率:0.4×n×(d/D+1) (d滚子直径,D节圆直径)
某案例中,通过800Hz处的边带波动(如图2),提前3周预警行星轮点蚀故障,避免非计划停机损失。
四、前沿技术应用趋势
数字孪生系统
构建减速机三维动力学模型,实时映射温度场、应力场分布(如图3)。某试验数据显示,虚拟调试使现场调试时间缩短70%。
永磁耦合技术
在输入轴加装永磁联轴器,可降低启动力矩65%,解决重载启动时的电流冲击问题。
复合衬套技术
采用铜基石墨镶嵌轴承,摩擦系数降至0.008,配合激光表面织构技术,使用寿命延长3倍。
五、能效提升实践案例
某年产百万吨水泥企业实施减速机改造项目:
更换为行星锥齿轮减速机
加装智能润滑单元
实施状态维修制度
改造后数据对比:
指标 |
改造前 |
改造后 |
提升幅度 |
电耗(kWh/t) |
4.8 |
4.2 |
12.5% |
故障停机(h/y) |
86 |
18 |
79% |
维护成本(万元) |
54 |
32 |
40.7% |
随着智能制造与绿色生产理念的深化,辊压机减速机正朝着高可靠性、智能化、节能化方向快速发展。通过精准选型、智能运维与技术创新,可显著提升粉磨系统综合效率,为工业企业创造更大价值。未来,集成物联网与人工智能的第四代减速机,将推动辊压机系统进入自主优化运行的新阶段。