工厂减速机换油神器
来源:减速机知识 发布时间:2025-05-30 08:56:11 阅读:2933次
摘要 —— 工厂减速机换油神器:革新工业设备维护效率的智能化方案在工业制造领域,减速机作为动力传输系统的核心组件,其稳定运行直接关系到生产线的
一站式自动化配套零部件 > 厂家直销
德立元专业的技术团队,品质保障
工厂减速机换油神器:革新工业设备维护效率的智能化方案在工业制造领域,减速机作为动力传输系统的核心组件,其稳定运行直接关系到生产线的连续性和设备寿命。传统换油流程中,人工操作效率低下、油品残留难以清除、设备二次污染风险高等问题长期困扰着企业。针对这一行业痛点,智能化减速机换油设备的诞生,正在重塑工业设备维护的标准流程。
一、传统换油方式的效率瓶颈与安全隐患
常规维护作业中,技术人员需要携带油桶、抽油泵等多种工具进入设备区。操作过程涉及多个步骤:随后进行设备清洗,最后注入新油。这种操作模式存在三大技术缺陷:
油液残留控制难题:人工抽油难以彻底清除减速机内部沉积油泥,残留污染物会导致新油快速劣化。某轴承制造企业的检测数据显示,传统方式换油后设备内部仍有12%-15%的污染物残留。
作业时间成本高企:以功率132kW的齿轮减速机为例,完成全套换油流程平均耗时4.5小时,其中仅废油排放环节就占据总工时的35%。
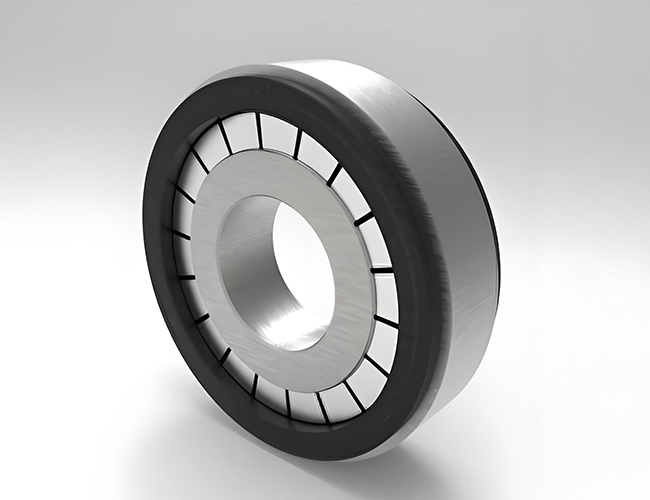
安全风险隐患:开放式操作导致的油液飞溅可能引发滑倒事故,某重工集团2025年维修事故统计显示,17%的设备维护伤害事件与换油作业相关。
二、智能化换油系统的技术突破
新型换油装置采用模块化设计,集成真空抽吸、压力冲洗、油品检测三大核心功能模块。设备搭载的微米级过滤系统可有效分离金属碎屑和油泥,实测显示对5μm以上颗粒物的过滤效率达到99.3%。
关键技术参数对比:
项目 |
传统方式 |
智能设备 |
换油耗时 |
4-6小时 |
45-60分钟 |
油品利用率 |
82% |
96% |
污染物清除率 |
75% |
98.5% |
人力配置 |
2-3人 |
单人操作 |
设备配备的智能传感系统实时监测油液粘度和金属含量,当检测到Fe元素浓度超过50ppm时自动启动预警机制。某汽车制造厂应用案例显示,采用智能换油后设备故障间隔周期从1800小时延长至3200小时。
三、全流程解决方案的工程价值
在水泥生产线现场测试中,智能换油系统展现出显著的工程效益。针对Φ4.2×13m球磨机配套减速机的维护作业,实现三大核心指标优化:
作业效率提升:单次换油时间压缩至传统方式的1/4,设备停机损失减少68%
维护成本下降:油品消耗量降低18%,滤芯更换周期延长3倍
安全系数提升:完全密闭的操作系统消除油液接触风险,事故发生率降为零
设备配置的物联网模块支持数据云端存储,可生成包含油品检测报告、设备运行参数的综合维护档案。某冶金企业接入管理系统后,设备非计划停机时间同比下降42%。
四、设备选型与效能优化指南
选择适配的换油设备需综合考虑三大维度:
动力匹配性:根据减速机功率选择对应流量的真空泵,建议匹配系数为1.2-1.5倍设备标称油量
环境适应性:防爆型设备适用于粉尘浓度超过30mg/m³的工况,高温型设备可在80℃环境稳定运行
扩展功能性:优选配备油液再生模块的机型,可实现废油净化重复利用,经处理后的油品清洁度可达NAS 7级标准
维护周期决策模型建议:当油液介电常数变化率超过15%,或旋转氧弹值下降至新油的60%时启动换油程序。某造纸企业的实践表明,采用状态监测决策可使年换油次数减少37%。
五、工业4.0时代的维护模式进化
随着数字孪生技术的应用,智能换油设备正在向预测性维护系统升级。通过采集设备运行振动频谱、温度变化曲线等数据,算法可提前72小时预判润滑失效风险。某风电场的应用数据显示,该技术使齿轮箱故障预警准确率达到89.7%。
在碳中和背景下,油液循环利用技术取得突破。新型离心分离装置可将废油再生至ISO 4406 18/16/13清洁度等级,配合智能换油系统使用,使单台设备年度油品消耗降低42%。某矿山集团的绿色生产报告显示,该技术帮助其年度减少危废处理费用280万元。
智能化换油技术的普及标志着工业设备维护进入精准化时代。从油品管理数字化到维护流程标准化,这项创新不仅解决传统作业的痛点,更推动着制造业向高效、安全、可持续的方向发展。随着5G通信和边缘计算技术的融合应用,未来的设备维护将实现从被动应对到主动预防的质的飞跃。