减速机齿轮比值
来源:减速机知识 发布时间:2025-05-23 15:43:37 阅读:2144次
摘要 —— 减速机齿轮比值的核心价值与工程应用解析在工业传动系统中,减速机作为动力转换的核心组件,其性能优劣直接影响着整条生产线的运行效率。齿
一站式自动化配套零部件 > 厂家直销
德立元专业的技术团队,品质保障
减速机齿轮比值的核心价值与工程应用解析在工业传动系统中,减速机作为动力转换的核心组件,其性能优劣直接影响着整条生产线的运行效率。齿轮比值作为减速机设计中的核心参数,不仅决定了设备的动力输出特性,更与设备寿命、能耗水平存在直接关联。本文将从技术原理、选型策略、维护要点三个维度,深度剖析减速机齿轮比值的关键作用。
一、齿轮比值的科学计算与参数优化
齿轮比值的精确计算建立在齿轮模数、齿数、分度圆直径等基础参数之上。以二级圆柱齿轮减速机为例,总传动比等于各级传动比的乘积,即i=i₁×i₂。工程实践中,设计者需根据输入转速(n₁)、输出转速(n₂)的工艺要求,通过公式i=n₁/n₂推导理论传动比,再结合标准齿轮参数进行匹配优化。
实际设计中需要重点考量三个制约因素:
热功率限制:高速级齿轮比过大会导致齿轮箱温升异常
结构紧凑性:多级传动中各级传动比的合理分配影响设备体积
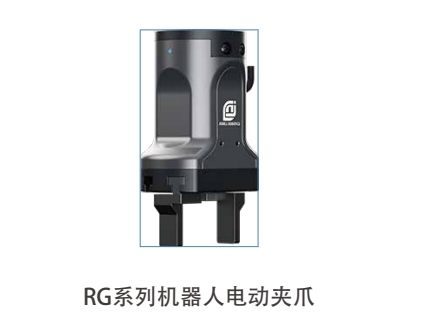
加工经济性:非标齿轮比值会显著增加制造成本
某水泥厂球磨机传动系统改造案例显示,通过将原设计的3.5:1单级传动改为1.8×1.9的二级传动结构,在保持总传动比不变的前提下,设备噪音降低8dB,轴承寿命延长40%。
二、齿轮比对设备性能的链式影响
齿轮比的微小调整可能引发设备性能的系统性变化。当传动比增大时,输出轴扭矩将呈线性增长,但转速下降曲线呈现非线性特征。以某型号行星齿轮减速器测试数据为例,传动比从10:1提升至15:1时,额定扭矩从1200N·m增至1850N·m,而效率曲线在传动比超过12:1后出现明显拐点。
在动态工况下,齿轮比的选择需特别注意:
冲击负载场景应保留15%-20%的扭矩裕度
频繁启停设备需控制传动比梯度,避免惯性冲击
精密传动系统要计算背隙对传动精度的影响系数
某自动化生产线改造项目中,通过将机械臂减速机的传动比从80:1优化至65:1,在保持定位精度的前提下,循环周期缩短0.3秒,年产能提升12万件。
三、多维度选型决策模型构建
减速机选型需建立系统化决策框架,除基本传动比参数外,还应综合评估:
负载特性矩阵
负载类型 |
建议传动比范围 |
润滑要求 |
恒定负载 |
10-30:1 |
ISO VG220 |
冲击负载 |
5-15:1 |
极压添加剂 |
交变负载 |
20-40:1 |
抗氧化配方 |
空间约束方程
当安装空间受限时,可采用谐波减速器或RV减速器,其单位体积传动比可达普通齿轮箱的3-5倍。某卫星天线驱动机构采用谐波减速器后,在Φ200mm空间内实现100:1传动比,重量减轻58%。
能效平衡点
通过建立传动比-效率-能耗的三角关系模型发现,当传动比处于设备最佳效率区间(通常为额定值的70-110%)时,系统综合能耗最低。某风电齿轮箱的实测数据显示,传动比偏离最优值10%时,年发电量损失达2.3%。
四、全生命周期维护技术要点
齿轮比值的稳定性取决于设备的维护水平。建议建立三级维护体系:
日常监测:使用振动分析仪检测齿频特征分量,当振幅超过基线值30%时预警
定期保养:每2000小时更换符合ISO 6743标准的润滑油,清洗磁性滤芯
大修标准:齿面点蚀面积超过20%或单个齿形误差超过DIN 3962三级精度时需返厂维修
某造纸企业通过实施油液颗粒度在线监测,将减速机故障率降低75%。其维护数据表明,保持润滑油清洁度在NAS 8级以内,可延长齿轮寿命周期30%以上。
五、前沿技术发展趋势
随着数字孪生技术的成熟,传动比优化进入智能化阶段。某汽车生产线采用虚拟调试系统,可在设备安装前完成传动比的多目标优化,使调试周期缩短40%。新材料方面,碳纤维增强尼龙齿轮已实现传动比50:1下的稳定运行,重量较钢制齿轮减轻60%。
在智能制造背景下,传动比的自适应调节成为新方向。磁流变流体齿轮箱原型机展示出传动比实时可调特性,调节范围可达1:5至1:20,为柔性化生产提供新的技术路径。
工业4.0时代,减速机齿轮比值的优化已从单一参数调整发展为系统级解决方案。工程师需要结合数字仿真、智能传感、新材料等跨领域技术,在传动效率、设备寿命、能耗成本之间建立动态平衡,推动工业传动系统向更高效、更智能的方向持续演进。