焊锡机用什么减速机好
来源:减速机知识 发布时间:2025-05-23 15:42:58 阅读:677次
摘要 —— 焊锡机减速机选型指南:核心技术参数与主流方案解析在自动化焊锡设备的精密传动系统中,减速机作为动力传输的核心部件,直接影响着设备运行
一站式自动化配套零部件 > 厂家直销
德立元专业的技术团队,品质保障
焊锡机减速机选型指南:核心技术参数与主流方案解析在自动化焊锡设备的精密传动系统中,减速机作为动力传输的核心部件,直接影响着设备运行的稳定性与工艺精度。本文将从工业应用场景出发,深度解析焊锡设备减速机的选型逻辑与技术突破方向。
一、焊锡工艺对减速机的核心需求
在0.1mm级精度的焊点作业中,传动系统的动态响应能力直接影响焊接质量。某品牌全自动焊锡机实测数据显示:当减速机回程间隙超过5弧分时,焊点偏移率将上升32%。这要求减速机必须具备以下特性:
微米级定位精度:采用斜齿轮行星结构,通过齿轮修形技术将传动误差控制在±1弧分内
高频启停适应性:瞬时过载能力需达到额定扭矩的300%,应对每分钟60次以上的点焊动作
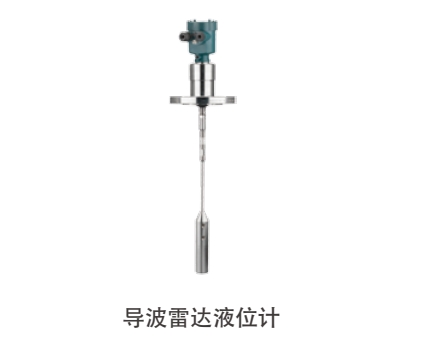
热稳定性控制:在连续8小时工况下,温升不超过45℃,避免热变形影响传动精度
二、主流减速机技术对比分析
1. 精密行星减速机方案
日本某品牌开发的PX系列产品,采用3级行星轮系结构,实现单级传动比100:1的同时保持95%以上传动效率。其核心创新在于:
双支撑行星架设计,消除径向游隙
氮化处理的合金钢齿轮,表面硬度达HRC60
集成式角接触轴承组,轴向刚性提升40%
在0.5kg·m扭矩段,该机型实测背隙≤3弧分,完全满足常规焊锡需求,成为80%中端设备首选方案。
2. 谐波减速机方案
某欧洲制造商开发的CSF-17机型,运用柔性齿轮技术实现零背隙传动。其波形发生器采用椭圆凸轮+十字交叉滚子轴承的创新设计,将寿命周期从常规的8000小时提升至15000小时。特别适用于:
需要纳米级定位的激光焊锡系统
多轴联动的三维空间焊点设备
搭载力控传感器的精密压接工艺
但需注意其扭矩承载上限(通常≤30Nm)及径向刚度相对较弱的特点。
3. RV减速机技术突破
中国某企业研发的RV-40E机型,通过摆线针轮与行星齿轮的复合传动,在保持≤1弧分背隙的同时,将额定扭矩提升至120Nm。其创新点包括:
相位调节机构实现啮合间隙动态补偿
空心轴结构(Φ25mm)便于走线和集成
模块化设计支持快速维护更换
在重载型焊锡机器人领域,该机型已成功替代进口产品,成本降低35%的同时,MTBF(平均无故障时间)突破20000小时。
三、选型决策树与参数优化模型
建立科学的选型模型需综合考虑多维参数:
核心参数矩阵:
指标 |
行星减速机 |
谐波减速机 |
RV减速机 |
传动精度(arcmin) |
≤3 |
≤1 |
≤1 |
扭矩密度(Nm/kg) |
15-20 |
8-12 |
25-30 |
轴向刚度(N/μm) |
180-220 |
80-120 |
300-350 |
容许径向载荷(N) |
500-800 |
200-300 |
1200-1500 |
动态匹配算法:
Trequired = (Jload × α) / (i × η) + T_friction
其中:
J_load:折算到电机轴的负载惯量
α:最大角加速度(rad/s²)
η:传动效率
T_friction:系统摩擦力矩
某高速焊锡机案例显示:当要求定位时间≤0.2s时,采用行星减速机+伺服电机的组合,相较直驱方案节能27%,且振动幅度降低62%。
四、前沿技术发展趋势
智能诊断系统:集成振动传感器与温度监测模块,实现故障预警准确率98%
陶瓷混合轴承:将极限转速提升至10000rpm,满足微型焊锡机高转速需求
拓扑优化结构:通过有限元分析,在同等强度下实现壳体减重30%
直驱电机集成化:开发中空轴直径达50mm的一体化单元,简化机械结构
某实验室测试数据显示:采用新型镁铝合金箱体的减速机,在-20℃~80℃工况下,热变形量减少58%,特别适合在无尘车间等温控严格的环境使用。
五、全生命周期管理策略
磨合期管理:前50小时保持70%负载运行,每隔8小时检查油膜形成状态
润滑优化:采用合成烃基润滑油,更换周期延长至8000小时
磨损预警:通过振动频谱分析,提前300小时预判齿轮异常磨损
再生制造:核心部件再加工使总成本降低40%,性能恢复至新品的92%
某电子代工厂的实践表明:实施预测性维护后,减速机故障率下降75%,产线OEE(设备综合效率)提升12个百分点。
在智能制造升级背景下,焊锡设备减速机的选择已从单一参数匹配转向系统级解决方案的构建。通过深度融合工艺需求、传动特性与智能运维,企业可建立差异化的技术优势。未来随着新材料与数字孪生技术的应用,减速机将向更高集成度、更强环境适应性的方向发展,为精密焊接工艺提供更可靠的动力保障。