伺服电机自带减速机吗
来源:减速机知识 发布时间:2025-05-17 18:13:30 阅读:3311次
摘要 —— 伺服电机是否自带减速机?深度解析结构与选型要点在工业自动化、机器人、精密制造等领域,伺服电机与减速机的组合是动力传递系统的核心单元
一站式自动化配套零部件 > 厂家直销
德立元专业的技术团队,品质保障
伺服电机是否自带减速机?深度解析结构与选型要点在工业自动化、机器人、精密制造等领域,伺服电机与减速机的组合是动力传递系统的核心单元。许多用户在设备选型时都会产生疑问:伺服电机是否自带减速机? 而是取决于具体产品设计及应用需求。本文将深入探讨伺服电机与减速机的结构关系、技术特点及选型策略,帮助建立清晰的认知体系。
一、伺服电机与减速机的协作关系
伺服电机以高精度位置控制、快速响应和闭环反馈为特点,但其本身输出转速高、扭矩低的特点,难以直接满足多数工业场景的需求。减速机的作用正是通过齿轮啮合或行星传动等方式,降低转速并放大扭矩,使伺服电机的输出特性与负载要求相匹配。
1. 集成式设计:一体化伺服减速电机
部分厂商推出将减速机直接嵌入伺服电机外壳的产品,例如:
采用行星减速箱与电机轴直连,缩短整体长度15%-30%
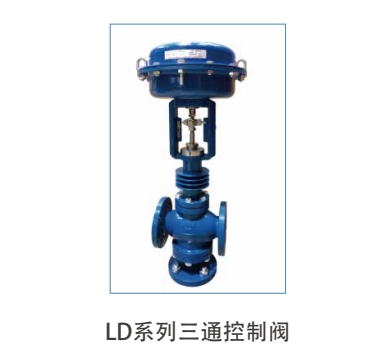
使用斜齿轮结构实现更高的扭矩密度(可达200Nm以上)
内置编码器反馈系统,保证减速后的定位精度(±1弧分以内)
这类一体化设备在AGV小车、协作机器人关节等空间受限场景中优势显著,但维护成本较高,需整体返厂维修。
2. 分体式设计:伺服电机+独立减速机
更多情况下,伺服电机与减速机作为独立单元组合使用:
通过法兰或联轴器连接,适配不同品牌的设备
支持模块化更换,例如谐波减速机、RV减速机可按需选配
维护时只需拆卸故障部件,降低停机成本
这种配置在注塑机、数控机床等大型设备中应用广泛,但需要额外考虑安装空间和传动效率损失(约3%-5%)。
二、集成式与分体式方案的技术对比
对比维度 |
集成式伺服减速电机 |
分体式伺服电机+减速机 |
传动效率 |
92%-95%(无中间连接损耗) |
88%-93%(存在联轴器损耗) |
安装空间 |
轴向长度缩短20%以上 |
需预留联轴器与安装基座空间 |
维护成本 |
整体更换成本高 |
可单独维修电机或减速机 |
扭矩密度 |
行星结构可达300Nm/kg |
谐波减速机扭矩密度约200Nm/kg |
适用场景 |
轻型机械臂、医疗设备 |
重载搬运、金属加工设备 |
三、典型应用场景的技术选型建议
1. 工业机器人关节驱动
协作机器人(6-10轴):优先选用集成式方案,例如采用谐波减速器的直驱电机,精度可达0.01°,满足柔性装配需求
重型搬运机器人:建议采用分体式RV减速机,其抗冲击能力是行星减速机的3倍以上
2. 精密数控设备
雕刻机主轴驱动:选用0背隙行星减速机,配合17位绝对式编码器,实现±0.005mm重复定位精度
五轴加工中心:推荐蜗轮蜗杆减速机,其自锁特性可防止断电时主轴下滑
3. 新能源设备
光伏板追日系统:采用IP67防护等级的集成式伺服减速电机,耐受-30℃至80℃环境温度
风力变桨系统:使用分体式方案,便于在塔顶更换故障减速机
四、选型决策的五大技术参数
减速比范围
根据电机额定转速(通常3000-6000rpm)与负载需求转速计算,常见减速比1:3至1:100。例如:
包装机械常用1:10-1:30
起重机卷扬机构需1:100以上
回程间隙指标
反映传动系统空转时的角度误差:
普通行星减速机≤8弧分
精密谐波减速机≤30弧秒
轴向/径向载荷
核查减速机轴承的承载能力:
行星减速机径向载荷一般≤2kN
RV减速机可承受≥5kN的冲击载荷
动态响应匹配
系统惯量比(负载惯量/电机转子惯量)建议控制在10:1以内,可通过减速比平方反比调节
热功率曲线
连续工作时应保证实际扭矩≤额定扭矩的80%,例如:
S5工作制(间歇运行)可承受120%过载
S1工作制(连续运行)需增加冷却装置
五、维护保养的关键要点
对于集成式伺服减速电机:
每2000小时检查润滑脂状态,使用NLGI 2级锂基脂
避免轴向冲击载荷,防止行星轮系卡死
定期用频闪仪检测输出端振动值,应≤4.5mm/s
分体式系统需特别注意:
联轴器对中误差控制在±0.05mm以内
每季度检测减速机油位,采用ISO VG320合成齿轮油
同步更换电机碳刷与减速机密封圈(如有)
六、技术发展趋势前瞻
直驱技术冲击
力矩电机直接驱动负载的方案正在侵蚀10-50Nm应用市场,但减速机在成本与扭矩密度上仍具优势
材料革新
SKD61渗氮钢齿轮寿命突破20000小时,陶瓷轴承使转速上限提升至10000rpm
智能诊断系统
集成振动传感器与温度监测模块,实现磨损程度的AI预测,例如:
通过FFT频谱分析提前3个月预警齿面点蚀
温升曲线异常提示润滑失效风险
伺服电机是否自带减速机,本质上是对系统集成度与可维护性的权衡。在高速高精的半导体设备中,一体化设计正在成为主流;而在重工业领域,分体式方案凭借其经济性和可靠性仍占据主导地位。用户应根据实际工况的扭矩、精度、空间限制等要素,结合全生命周期成本进行综合判断。随着机电一体化技术的进步,未来可能出现更多突破传统界限的创新解决方案。