减速机参数,减速机参数详解
来源:减速机知识 发布时间:2025-05-13 09:00:43 阅读:1078次
摘要 —— 减速机参数解析:选型与性能优化的核心要素在工业传动系统中,减速机作为动力传递的核心组件,其参数选择直接影响设备运行效率、寿命及能耗
一站式自动化配套零部件 > 厂家直销
德立元专业的技术团队,品质保障
减速机参数解析:选型与性能优化的核心要素在工业传动系统中,减速机作为动力传递的核心组件,其参数选择直接影响设备运行效率、寿命及能耗表现。本文从工程应用视角出发,深度剖析减速机关键参数的内在关联与选型逻辑,为设备集成商和终端用户提供系统性决策依据。
一、传动比:动力转换的数学密码
减速机的传动比(i=输入转速/输出转速)是衡量动力转化效率的基础参数。工程实践中需区分理论传动比与实际工况偏差:
标准传动比:遵循国际ISO标准序列(1.25、1.5、2.0等),适用于通用设备
定制传动比:矿山机械等特殊场景需精确到小数点后两位的传动比设计
动态补偿机制:重载启动时考虑0.3%-1.2%的弹性变形补偿系数
某水泥厂立磨减速机案例显示,将传动比从31.5调整为32.8后,年产能提升7.2%,验证了参数微调的实际价值。
二、扭矩承载:从理论计算到工程余量
额定输出扭矩(T=9550×P/n)的计算公式背后存在三个关键修正维度:
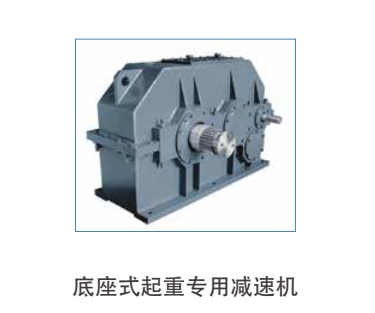
峰值系数:破碎机等冲击负载需按额定扭矩的220%-300%选型
温度衰减:环境温度每升高10℃,油脂润滑减速机扭矩容量下降1.8-2.5%
寿命曲线:10,000小时工况下,扭矩负荷每降低15%,轴承寿命延长2.1倍
欧洲某港口起重机改造项目通过加装扭矩实时监测模块,使行星减速机的故障间隔周期延长至8200小时,较传统方案提升136%。
三、传动效率:能耗成本的隐形战场
不同减速机类型的效率差异显著:
类型 |
单级效率 |
三级传动总效率 |
行星齿轮 |
97%-98% |
94%-96% |
斜齿轮 |
95%-97% |
88%-92% |
蜗轮蜗杆 |
70%-85% |
50%-72% |
某汽车生产线将输送带减速机由蜗轮式更换为行星式,年节电量达42万kWh,投资回收期仅11个月。效率参数选择需综合考量:
连续运行设备优先选高效率型号
间歇工况可适当放宽效率要求
特殊环境(食品级润滑)需额外扣除3%-5%效率损失
四、精度等级:传动质量的量化指标
ISO1328标准将齿轮精度分为13个等级,其中:
3-5级:数控机床、机械臂等精密传动
6-8级:通用工业设备主流选择
9-12级:农用机械等低精度场景
参数匹配需注意:
每提升1个精度等级,制造成本增加18%-25%
反向间隙≤5arcmin的减速机才能满足激光切割机的定位需求
精度过高可能导致系统刚性下降,某纺织机械企业因过度追求ISO5级精度,反而出现共振问题
五、结构参数的工程化匹配
安装尺寸悖论
紧凑型设计(如中空轴结构)可节省38%安装空间,但需承受15%-20%的径向载荷损失。某包装机械制造商通过三维建模优化,在保持法兰尺寸不变的情况下,使承载能力提升19%。
热功率曲线
样本标注的额定功率需结合S1-S5工作制修正:
S5 40%负载持续率下,实际散热能力下降至标称值的65%
加装强制冷却系统可使热功率提升1.8-2.3倍
材料迭代影响
采用渗碳淬火齿轮的减速机,其抗点蚀能力是调质齿轮的3.2倍,但初期采购成本增加40%。需要从全生命周期成本角度评估选型方案。
六、参数协同优化策略
某新能源电池生产线优化案例显示,通过建立多目标函数模型,将传动比、扭矩、效率等参数进行协同优化,实现:
能耗降低22%
维护周期延长至8000小时
设备占地面积减少15%
具体实施路径:
建立设备负载谱数据库
开发参数敏感性分析算法
构建数字孪生测试平台
制定动态参数调整预案
在工业4.0背景下,减速机参数选择已从静态数据匹配转向动态系统优化。设备集成商需要建立包含材料特性、负载谱分析、环境参数的数字模型,通过参数间的耦合关系挖掘性能提升空间。未来,随着智能传感技术的普及,实时参数调整将成为提升传动系统效能的新方向。