维修摆针式减速机
来源:减速机知识 发布时间:2025-05-08 08:52:06 阅读:4198次
摘要 —— 维修摆针式减速机的核心技术与实践指南摆针式减速机作为工业传动领域的核心部件,其稳定运行直接影响生产线效率与设备寿命。然而,长期高负
一站式自动化配套零部件 > 厂家直销
德立元专业的技术团队,品质保障
维修摆针式减速机的核心技术与实践指南摆针式减速机作为工业传动领域的核心部件,其稳定运行直接影响生产线效率与设备寿命。然而,长期高负荷运转或操作不当易引发机械磨损、密封失效等问题。本文将深入探讨摆针式减速机维修的关键技术,从故障诊断、拆装规范到维护策略,为技术人员提供系统化的解决方案。
一、常见故障诊断与精准分析
1. 异常振动与噪音
设备运转时出现周期性异响或高频振动,通常与摆线轮磨损、轴承间隙异常相关。通过频谱分析仪检测振动频率,若发现特征频率与摆线轮啮合频率重合,需重点检查轮齿表面是否出现剥落、点蚀现象。
处理方案:
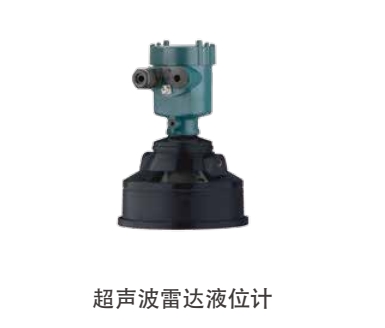
拆卸后使用磁粉探伤仪检测摆线轮裂纹
更换磨损轴承时需同步测量壳体同轴度
安装新齿轮后进行空载磨合测试
2. 润滑油泄漏问题
输出端密封处出现油渍或油滴,可能源于骨架油封老化、密封面划伤。需注意观察泄漏位置是否伴随箱体温度异常升高,排除润滑油过量或粘度不符导致的压力失衡。
关键检查点:
密封槽尺寸精度(建议使用三坐标测量仪)
轴承室端面跳动量(标准值≤0.05mm)
透气阀堵塞状态(维护时需用压缩空气疏通)
3. 传动效率下降
设备出现启动困难、输出扭矩不足时,应重点检测摆线轮与针齿壳的配合间隙。使用塞尺测量径向间隙,当数值超过原设计值30%时,需更换磨损件。
技术规范:
部件名称 |
允许磨损量 |
检测工具 |
摆线轮齿面 |
≤0.15mm |
轮廓投影仪 |
针齿销 |
≤0.08mm |
千分尺 |
输出轴键槽 |
≤0.1mm |
游标卡尺 |
二、标准化维修操作流程
1. 系统化拆解规范
使用液压拉马拆卸输入轴联轴器,禁止火焰加热
箱体分解前做好各部件位置标记(建议激光打标)
精密部件存放需使用防锈油纸包裹
2. 核心部件修复技术
(1)摆线轮修复
轻微磨损采用低温冷焊工艺修补
齿形修正需使用五轴数控磨床加工
表面进行渗氮处理(硬度需达HRC58-62)
(2)轴承室修复
磨损量0.3mm内采用高分子金属修补剂
超过公差范围时使用激光熔覆技术
修复后需进行24小时恒温时效处理
3. 高精度装配要点
分阶段预紧偏心轴承(先预紧60%,运行测试后二次紧固)
采用动态扭矩扳手控制输入轴锁紧螺母(扭矩值参照设备铭牌120%)
装配完成后进行三级测试:
空载运行(检测振动值≤4.5mm/s)
负载测试(逐级加载至额定功率)
热成像检测(各部件温升≤35℃)
三、预防性维护策略
1. 智能监测体系构建
安装在线油液监测传感器(检测铁屑含量>100ppm时预警)
配置振动分析系统(设置ISO10816-3报警阈值)
建立设备健康档案(记录每次维修数据形成趋势图)
2. 润滑管理优化
选用合成型极压齿轮油(黏度等级根据环境温度选择)
注油时采用真空滤油设备(清洁度达NAS7级标准)
建立油脂更换周期矩阵:
工作温度 |
连续运行周期 |
冲击负荷工况 |
<50℃ |
4000小时 |
3000小时 |
50-80℃ |
2500小时 |
2000小时 |
>80℃ |
1500小时 |
立即更换 |
3. 操作规范培训
禁止在超载10%以上工况连续运行超过30分钟
启停间隔需>5分钟(防止润滑油未充分回流)
异常情况处理流程:
1) 立即切换备用设备
2) 记录故障代码与运行参数
3) 联系专业团队进行失效分析
四、技术创新与维修升级
引入3D扫描技术逆向建模,对比设计图纸生成部件磨损云图。对于批量设备,建议采用再制造工艺:通过数控加工中心修复箱体基准面,配合定制化衬套恢复原始配合公差。经实测,该方案可使维修成本降低40%,设备寿命延长60%。
掌握摆针式减速机维修技术需要理论结合实践,建议企业建立PDCA循环改进机制:每次维修后分析根本原因,优化维修方案。定期使用频闪仪观察运转状态,结合油液铁谱分析预判故障,真正实现从被动维修到主动防护的转变。通过实施本方案,某水泥企业成功将减速机故障停机时间从年均120小时降至18小时,验证了系统化维修管理的显著成效。