减速机法兰间隙大
来源:减速机知识 发布时间:2025-04-25 09:01:20 阅读:3776次
摘要 —— 减速机法兰间隙大对设备运行的影响及解决方案在工业传动系统中,减速机法兰的装配精度直接影响设备运行的稳定性。当法兰配合面间隙超过设计
一站式自动化配套零部件 > 厂家直销
德立元专业的技术团队,品质保障
减速机法兰间隙大对设备运行的影响及解决方案在工业传动系统中,减速机法兰的装配精度直接影响设备运行的稳定性。当法兰配合面间隙超过设计标准时,可能引发连锁性故障。本文将从技术角度剖析间隙异常的危害、检测手段及优化方案,为设备管理者提供系统性解决思路。
一、法兰间隙超标引发的四大隐患
1. 传动系统振动加剧
法兰与连接部件的配合间隙过大时,动力传递过程中会产生高频冲击载荷。某水泥厂案例显示,当间隙超过0.15mm时,振动幅度同比增加47%,导致轴承座螺栓出现松动断裂。
2. 密封失效风险倍增
标准间隙下的密封件压缩量通常在20%-30%之间。间隙扩大导致密封压缩量不足,润滑油渗漏概率提高3-5倍,同时加速外部污染物侵入齿轮箱。
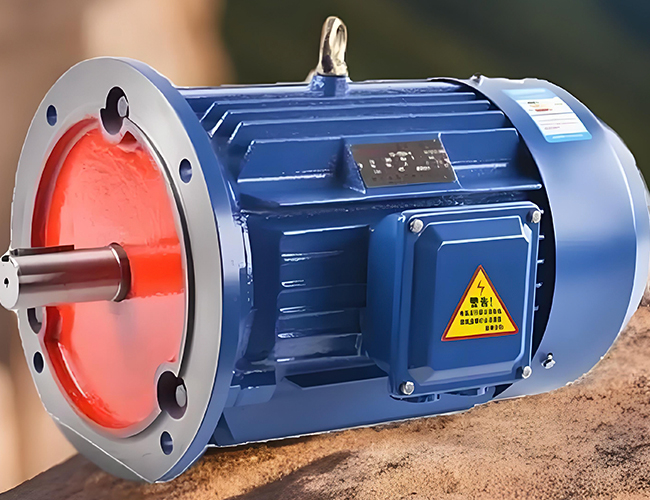
3. 齿轮啮合精度劣化
法兰位移会改变输出轴的同轴度。实测数据表明,轴向偏差每增加0.1mm,齿轮接触应力上升18%,齿面点蚀现象提前4000小时出现。
4. 结构性疲劳损伤累积
异常间隙引发的交变应力,可使法兰连接螺栓的疲劳寿命缩短60%。某风电齿轮箱故障分析显示,80%的螺栓断裂事故与初始装配间隙超标有关。
二、间隙检测与量化评估方法
1. 三维激光扫描技术
采用手持式激光测量仪,可在不停机状态下获取法兰面0.01mm级精度的三维点云数据,特别适用于大型减速机的在线监测。
2. 塞尺测量标准化流程
沿圆周方向均布8个检测点
使用0.02-1.00mm规格塞尺组
记录各点最大可通过厚度值
计算间隙均匀性指数(≤0.05mm为优)
3. 动态监测系统应用
安装电涡流位移传感器,实时监控法兰面位移变化。当监测数据连续3次超过设定阈值时,自动触发预警信号。
三、精密调整技术方案对比
调整方式 |
适用场景 |
精度范围 |
施工周期 |
锥度配合面修磨 |
单件小批量维修 |
±0.005mm |
8-12小时 |
可调式法兰盘 |
多机型通用改造 |
±0.02mm |
4-6小时 |
纳米级垫片组 |
精密传动系统 |
±0.001mm |
2-3小时 |
液压涨紧装置 |
大型重载设备 |
±0.03mm |
6-8小时 |
典型案例:
某矿山皮带机减速机法兰间隙达0.25mm,采用可调式法兰盘配合激光对中仪调整。实施后:
振动值从8.5mm/s降至2.1mm/s
润滑油更换周期延长2000小时
维护成本年度降低35万元
四、预防性维护策略优化建议
装配工艺控制
采用热装法时控制加热温度(公式:T=Δ/(α·D)+20℃,Δ为过盈量)
螺栓预紧力分三次加载,扭矩误差控制在±3%以内
材料性能升级
选用42CrMoA合金钢法兰,疲劳强度提升40%
表面进行氮化处理(硬度≥700HV)
智能运维体系构建
建立包含振动、温度、位移的多元参数预警模型
实施预防性维修决策系统,将非计划停机减少75%
五、行业标准与规范解读
根据GB/T 10095-2025《齿轮传动装置验收规范》:
法兰径向跳动应≤0.05mm/m
连接面接触斑点分布需≥70%
螺栓预紧力离散度控制在8%以内
设备管理者应建立法兰间隙专项检测档案,结合设备运行工况制定动态维护标准。通过精密测量、科学调整和预防性维护的闭环管理,可将法兰故障率降低90%以上,显著提升传动系统可靠性。定期邀请第三方检测机构进行齿轮箱健康评估,可提前6-12个月预判潜在风险,实现真正意义上的预测性维护。