撕碎机减速机装配
来源:减速机知识 发布时间:2025-04-23 09:16:47 阅读:696次
摘要 —— 撕碎机减速机装配工艺解析与质量控制要点在固废处理、资源回收等领域,撕碎机作为核心设备承担着物料破碎的关键任务。减速机作为撕碎机动力
一站式自动化配套零部件 > 厂家直销
德立元专业的技术团队,品质保障
撕碎机减速机装配工艺解析与质量控制要点在固废处理、资源回收等领域,撕碎机作为核心设备承担着物料破碎的关键任务。减速机作为撕碎机动力传输的核心部件,其装配质量直接影响设备运行效率与使用寿命。本文从装配工艺、精度控制、常见问题排查三个维度,系统解析撕碎机减速机的科学装配方法。
一、减速机装配前的关键准备工作
1.1 零部件清洁与检测
装配前需对所有零部件进行深度清洁,重点去除齿轮箱壳体、轴承座等部位的加工残留物。使用工业清洗剂配合超声波设备处理齿轮、轴类零件表面,确保配合面无油污、金属碎屑。同步开展尺寸复测,利用三坐标测量仪验证齿轮模数、齿面粗糙度是否符合GB/T 10095标准。
1.2 装配环境控制
建立恒温恒湿装配车间(温度控制在20±2℃,湿度≤60%),避免温差导致的金属部件热胀冷缩。地面安装防静电地坪,操作台配置磁性隔离垫,防止铁屑污染精密部件。
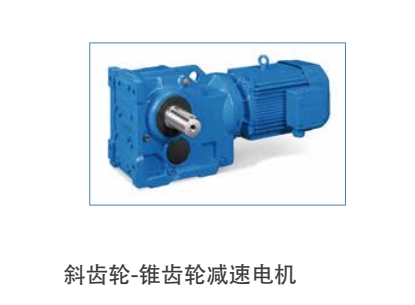
二、核心装配流程与技术规范
2.1 箱体-齿轮轴配合工艺
采用热装法安装轴承:将轴承加热至80-100℃后快速装入箱体轴承室,利用热胀冷缩原理实现过盈配合。关键控制点包括:
加热温度偏差不超过±5℃
轴向预紧力控制在设计值的90-110%
齿轮副侧隙检测需使用铅丝压痕法,确保0.12-0.25mm标准间隙
2.2 行星轮系装配要点
针对行星架组件装配,需遵循"三点定位"原则:
行星轮与太阳轮啮合斑点需覆盖齿面70%以上
行星轮轴向游隙控制在0.03-0.05mm
行星架端面跳动量≤0.02mm/Φ200
使用扭矩倍增器分阶段紧固螺栓,初始预紧力为额定值的30%,最终分三次递增至设计扭矩,每次间隔10分钟释放应力。
三、装配过程中的典型问题与解决方案
3.1 振动异常诊断流程
现象特征 |
可能原因 |
解决措施 |
轴向振动>5mm/s |
轴承预紧力不足 |
重新调整圆锥滚子轴承轴向间隙 |
径向振动异常 |
齿轮啮合不良 |
激光对中仪校正输入/输出轴同心度 |
高频异响 |
润滑脂污染 |
更换ISO VG320合成齿轮油 |
3.2 过热问题处理方案
当减速机温升超过45K时,应执行三级排查:
红外热成像仪扫描发热点
检查润滑油粘度(40℃时需达288-352 cSt)
验证散热系统风量(≥200m³/h)
四、装配质量验证体系
4.1 动态测试标准
空载测试阶段:
连续运行2小时,温升≤35K
噪声值≤78dB(A)(距设备1m处测量)
负载测试要求:
逐级加载至120%额定扭矩,持续30分钟
齿轮箱振动速度有效值≤4.5mm/s
4.2 数据化验收标准
建立装配质量数据库,记录关键参数:
齿轮接触斑点图像(存档分辨率≥300dpi)
轴系对中数据(允许偏差≤0.05mm/m)
螺栓紧固力矩曲线图
五、长效维护管理策略
实施预防性维护制度:
首次运行500小时后更换润滑油
每季度检测齿轮磨损量(允许最大磨损0.02mm/年)
采用油液颗粒计数器监控润滑油清洁度(NAS 8级标准)
引入智能监测系统:
在减速机关键位置安装振动传感器、温度变送器,通过物联网平台实现:
振动频谱实时分析
温度趋势预测
故障代码自动诊断
通过科学的装配工艺与严格的质量控制,可使撕碎机减速机的运行寿命提升30%以上。建议企业建立标准化装配作业指导书(WI),定期对装配人员进行技能认证(参照ISO/TR 10000标准),持续优化装配质量体系。在智能制造趋势下,结合数字孪生技术进行虚拟装配验证,将成为提升装配精度的新方向。