偏航电机减速机
来源:减速机知识 发布时间:2025-04-21 08:52:21 阅读:3436次
摘要 —— 偏航电机减速机:风电设备精准控制的核心技术在风力发电领域,偏航系统是保障风机高效运转的关键部件,而偏航电机减速机作为其核心驱动装置
一站式自动化配套零部件 > 厂家直销
德立元专业的技术团队,品质保障
偏航电机减速机:风电设备精准控制的核心技术在风力发电领域,偏航系统是保障风机高效运转的关键部件,而偏航电机减速机作为其核心驱动装置,直接影响着风电机组的稳定性与能量转化效率。随着全球风电装机容量持续增长,市场对高精度、高可靠性的偏航电机减速机需求日益迫切。本文将从技术原理、应用场景、选型要点及行业趋势等维度,深度解析这一核心设备的价值与发展方向。
一、偏航电机减速机的工作原理与技术创新
偏航电机减速机通过多级齿轮传动系统,将电机输出的高转速低扭矩转化为低转速高扭矩动力,驱动风机机舱精准调整角度,使叶片始终垂直迎风面。其核心技术体现在三方面:
精密齿轮设计
采用行星齿轮、斜齿轮或蜗轮蜗杆结构,通过优化齿形参数(如压力角、模数)与表面硬化处理,实现传动效率≥96%、噪音≤65dB。例如,某型号减速机通过非对称齿廓设计,将齿面接触应力降低30%,显著延长使用寿命。
动态载荷适应性
针对风速突变导致的冲击载荷,新一代减速机集成扭矩限制器与弹性联轴器。实验数据显示,在8级阵风工况下,此类设计可将齿轮箱振动幅度控制在0.05mm以内,避免因过载造成的齿轮断裂风险。
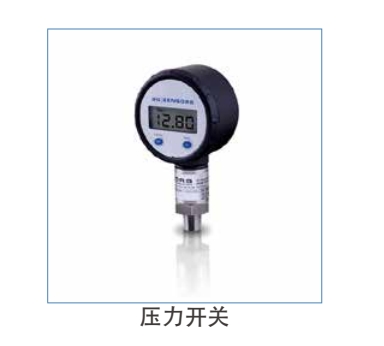
智能监测系统
内置温度、振动传感器与物联网模块,实时采集油温、齿轮啮合状态等数据。某风场案例显示,通过预测性维护系统,设备故障率下降45%,运维成本减少28%。
二、应用场景与性能需求差异分析
不同环境与机型对偏航电机减速机的性能提出差异化要求:
场景分类 |
技术指标要求 |
典型案例 |
陆上大型风电机组 |
扭矩范围20-50kN·m,防护等级IP65 |
5MW机组匹配三级行星减速机 |
海上漂浮式风机 |
抗盐雾腐蚀,轴向载荷承载能力≥80kN |
10MW机组采用不锈钢蜗轮蜗杆结构 |
高海拔低温风场 |
低温型润滑脂(-40℃工况),密封防冻设计 |
青藏高原风场使用特种复合材料箱体 |
以海上风电为例,减速机需通过ISO 12944 C5-M防腐认证,并采用双密封圈结构防止海水渗透。某欧洲厂商开发的钛合金齿轮箱,在北海风场实现15年零故障运行记录。
三、选型决策中的关键参数与验证方法
选择适配的偏航电机减速机需综合考量以下核心参数:
扭矩与速比匹配
根据风机转子直径计算偏航阻力矩:
[ T = frac{1}{2} rho Cd A v^2 R ]
其中,ρ为空气密度,Cd为阻力系数,A为迎风面积,v为风速,R为力臂长度。通过动态仿真确定速比范围(通常1:50至1:200),避免电机频繁启停。
材料与工艺验证
齿轮材质:18CrNiMo7-6渗碳钢,表面硬度≥58HRC
箱体铸造:采用消失模工艺,尺寸精度达CT6级
第三方检测报告需包含:
2000小时满载耐久测试
盐雾试验≥720小时无锈蚀
温升测试(油温≤85℃)
能效与经济性平衡
对比全生命周期成本(LCC),包括采购成本、维护费用与发电损失。研究表明,选用高精度减速机虽初始投资增加15%,但年均发电量提升3.2%,投资回收期缩短至2.8年。
四、行业技术演进与未来挑战
轻量化与集成化趋势
碳纤维复合材料齿轮箱较传统钢制结构减重40%,同时通过电机-减速机一体化设计(如法兰直连结构),减少30%安装空间。德国Fraunhofer研究所已开发出模块化减速单元,支持快速更换故障组件。
数字孪生技术应用
基于数字孪生模型的虚拟调试技术,可在设备安装前模拟不同风速、载荷下的运行状态。某制造商应用该技术后,现场调试时间缩短60%,偏航角度误差控制在±0.5°以内。
极端环境适应性突破
针对北极圈-50℃超低温环境,研发耐寒润滑脂与加热型箱体;针对沙漠风沙环境,开发多级过滤通风系统,防止颗粒物进入齿轮啮合面。
五、运维优化策略与标准体系
建立科学的运维体系是保障设备可靠性的关键:
预防性维护周期:每12个月更换润滑脂,每5年开箱检查齿轮磨损(使用内窥镜技术)
故障诊断标准:振动速度有效值>4.5mm/s时触发预警,齿面点蚀面积>6%需立即更换
再制造技术:采用激光熔覆修复齿面磨损,成本较新购设备降低50%
国际电工委员会IEC 61400-4标准明确规定了偏航减速机的测试方法与性能阈值,厂商需通过GL、DNV等权威认证以进入全球供应链。
在碳中和目标推动下,偏航电机减速机正朝着智能化、高可靠方向快速迭代。从材料创新到数字赋能,这一领域的技术突破将持续提升风电机组的发电效率与运行寿命,为可再生能源发展注入核心驱动力。