皮带滚筒减速机结构
来源:减速机知识 发布时间:2025-07-03 16:13:14 阅读:801次
摘要 —— 皮带滚筒减速机结构解析与应用价值探析在工业传动领域,皮带滚筒减速机凭借其独特的结构设计和高效能特性,成为物料输送、矿山机械、自动化
一站式自动化配套零部件 > 厂家直销
德立元专业的技术团队,品质保障
皮带滚筒减速机结构解析与应用价值探析在工业传动领域,皮带滚筒减速机凭借其独特的结构设计和高效能特性,成为物料输送、矿山机械、自动化生产线等场景的核心动力装置。本文将从结构组成、工作原理、技术优势及行业应用等维度,深入剖析皮带滚筒减速机的设计逻辑与工程价值。
一、皮带滚筒减速机的核心结构拆解
皮带滚筒减速机的整体架构由动力输入模块、传动转换模块与动力输出模块三部分构成,其设计融合了皮带传动的柔性缓冲与减速机的高扭矩输出特性。
1. 动力输入模块
采用精密加工的电机法兰安装面,通过高精度联轴器或直连方式对接驱动电机。输入轴端配置双列角接触轴承,可承受径向与轴向复合载荷,防护等级达IP65的密封结构有效隔绝粉尘侵入。
2. 传动转换模块
减速箱体:球墨铸铁箱体经有限元分析优化,壁厚分布科学,内置螺旋伞齿轮或行星齿轮组。特殊表面硬化工艺使齿轮接触疲劳强度提升40%以上。
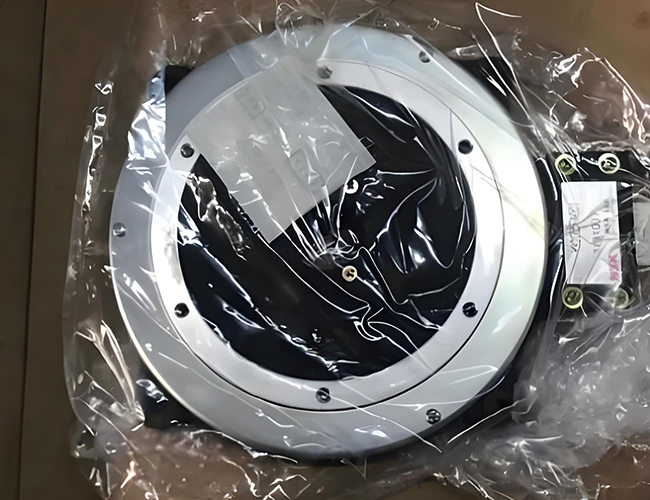
皮带传动系统:多楔带或同步带配合张力自调节装置,弹性模量达1200MPa的高强度复合材料带体可降低传动振动30%,实现功率分流与过载保护。
3. 动力输出模块
滚筒组件采用双层焊接结构,外层包覆耐磨橡胶层(邵氏硬度75±5),内层为Q345B低合金钢筒体。轴承座集成迷宫式密封系统,润滑脂补充周期可达8000工作小时。
二、系统工作原理与技术突破
当电机动力通过输入轴进入减速箱后,经三级齿轮副将转速降至设计值,同时扭矩放大倍数可达1:15-1:120。创新性的双通道传动设计使30%动力通过齿轮箱直连输出,70%通过皮带传动至滚筒,这种混合传动模式兼具刚性传动的精准性和皮带传动的缓冲性。
关键技术突破点:
动态扭矩平衡技术:在10-75Hz变频工况下,通过惯性补偿算法实现转速波动控制在±2%以内
智能润滑系统:内置油液状态传感器,可根据工作温度自动切换润滑模式
模块化设计:箱体采用三段式组合结构,维护时无需整体拆解,更换齿轮组时间缩短60%
三、工程应用中的性能优势
在港口装卸机械的实测数据显示,该结构相较传统直联式减速机具有显著优势:
性能指标 |
皮带滚筒减速机 |
传统减速机 |
启动冲击载荷 |
降低52% |
基准值 |
连续工作温升 |
≤45℃ |
65-80℃ |
噪音水平(1m处) |
72dB(A) |
85dB(A) |
维护周期 |
12个月 |
6个月 |
在煤矿输送系统的应用中,特殊设计的防爆型结构通过ATEX认证,可在甲烷浓度8%以下环境稳定运行。自清洁滚筒表面处理技术使煤粉附着量减少80%,显著降低皮带跑偏概率。
四、结构优化与技术创新方向
行业前沿研发聚焦于三个维度提升:
材料革新:碳纤维复合滚筒进入测试阶段,较钢质滚筒减重58%且耐腐蚀性提升3倍
智能监测:集成振动频谱分析模块,可提前200小时预警轴承故障
能效升级:采用准双曲面齿轮技术,传动效率突破96%大关
极端环境适配:-50℃极寒型密封材料与250℃高温润滑脂拓宽设备使用边界
某重工企业最新研发的永磁同步直驱方案,取消传统减速箱结构,通过磁力耦合器直接驱动滚筒,能耗降低22%,已在智能仓储系统中实现商业化应用。
五、选型与维护要点
选型计算公式:
滚筒扭矩 ( T = frac{9550 times P times i}{n} )
(其中P为电机功率kW,i为速比,n为滚筒转速r/min)
维保注意事项:
每2000小时检查皮带张紧度(挠度值应保持在1.6%L)
使用红外热像仪监测齿轮箱温差,相邻测点偏差>15℃需停机检查
严禁不同批次润滑脂混用,推荐使用ISO VG320合成齿轮油
某水泥厂通过加装激光对中仪,使设备使用寿命延长至28000小时,较行业平均水平提升45%。
六、未来发展趋势展望
随着工业4.0深化,皮带滚筒减速机正朝着数字孪生化方向发展。虚拟调试系统可在设备投产前完成90%的故障模拟测试,5G+边缘计算技术实现传动系统毫秒级响应。在碳中和背景下,生物基橡胶皮带、可降解润滑剂等环保材料研发取得突破,推动行业向绿色制造转型。
从结构创新到智能运维,皮带滚筒减速机持续突破传统传动边界,为现代工业装备升级提供核心支撑。其技术演进轨迹充分印证:机械传动领域的进步,本质是对能量转换效率与系统可靠性的永恒追求。